
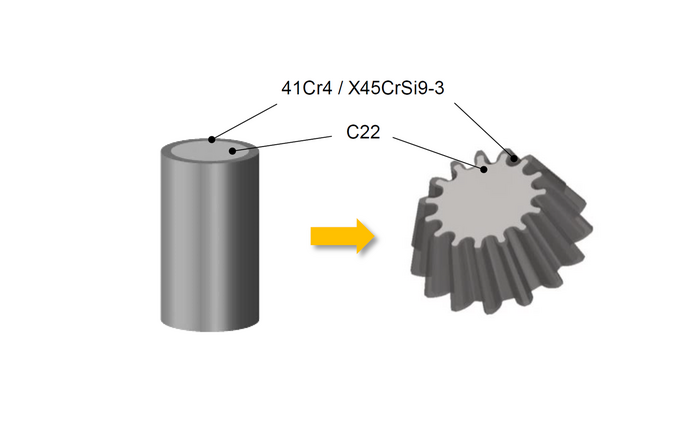
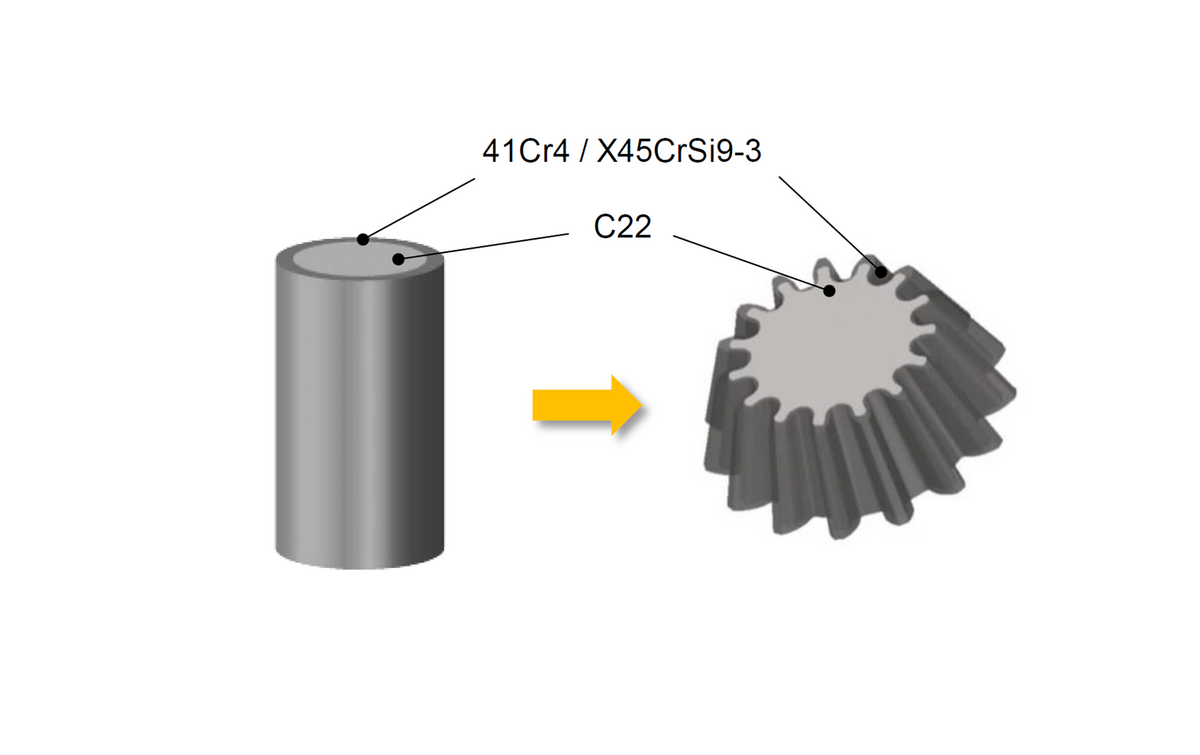
Motivation and objectives
The aim of the subproject C07 is the development of a new system for the safe and precise handling of tailored forming components with different geometries and surface temperatures from over 300°C up to 1250°C. Such a gripping system will be developed in close cooperation with the subprojects B02, B03 and C05, which specify the system requirements. A special requirement, in addition to shape variability and temperature resistance, is the ability to cool the gripped objects. This enables an improved joining zone through the specific adjustment of temperature gradients in the components, which is component-dependent and not necessary for every material combination, thus pursuing a modular design. Figure 2 shows the handling process during the forming process. In addition, it is shown which properties are required for the gripper system in the individual process steps. The shape variability is important when an object is gripped. The forming process results in considerable variations from the cylindrical shape of the semi-finished products, which must be adapted by the gripper. The temperature resistance is indispensable for the rest of the process after heating, since the temperatures do not drop back to ambient temperature until the next process. The research hypothesis is that this enables efficient and process-adapted gripper development with a special focus on the requirements of the tailored forming process chain
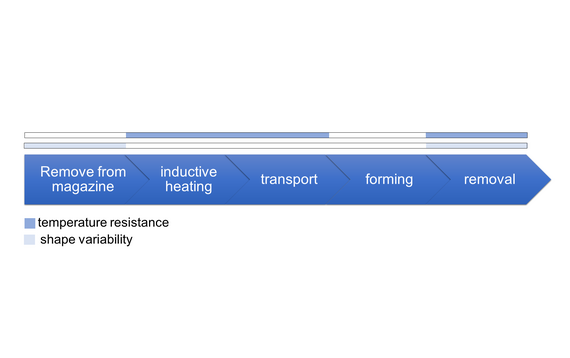
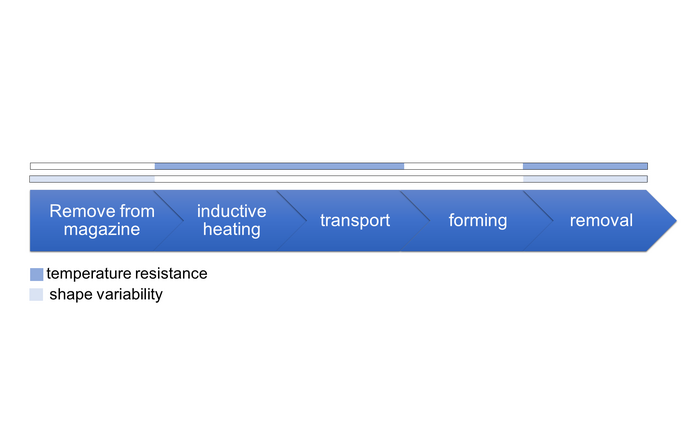
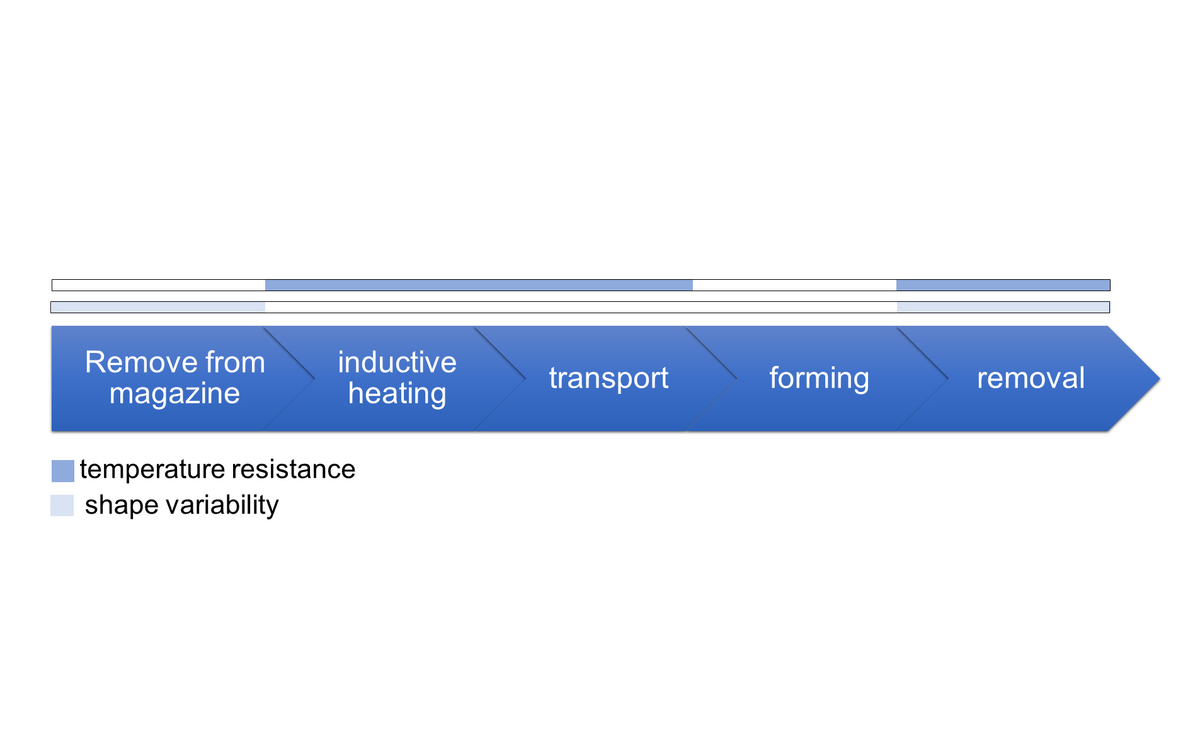
Current work and outlook
A concept for a form variable gripping system is currently being developed which meets the required conditions, temperature resistance and cooling option. Research has shown that form variable grippers consist mainly of soft skins filled with a medium that adapts to the shape of the object to be gripped. The materials used are limited in their operating temperature, so that a high-temperature operation is not practicable. Only a form variable gripper based on the matrix system shows potential. This uses pins that are axially movable to adapt the negative contour of an object. The concept offers the possibility to consider a wide range of materials that match the operating conditions. Figure 3 shows a current concept study where a gripper is illustrated inside a forming machine based on the matrix system.
In order to ensure the modular design of the system, parallel work is being carried out on a cooling unit. This should make it possible to achieve the required temperature profiles, required by subprojects B2 and B3, in the components in order to increase the quality of the joining zone. To this end, various cooling principles will be investigated and the necessary cooling capacity will be designed in cooperation with the subproject C4 and integrated into the gripping system.
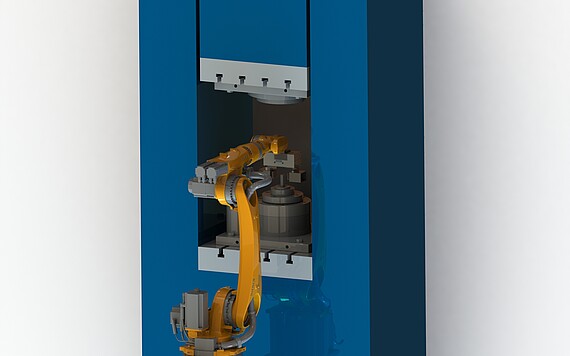

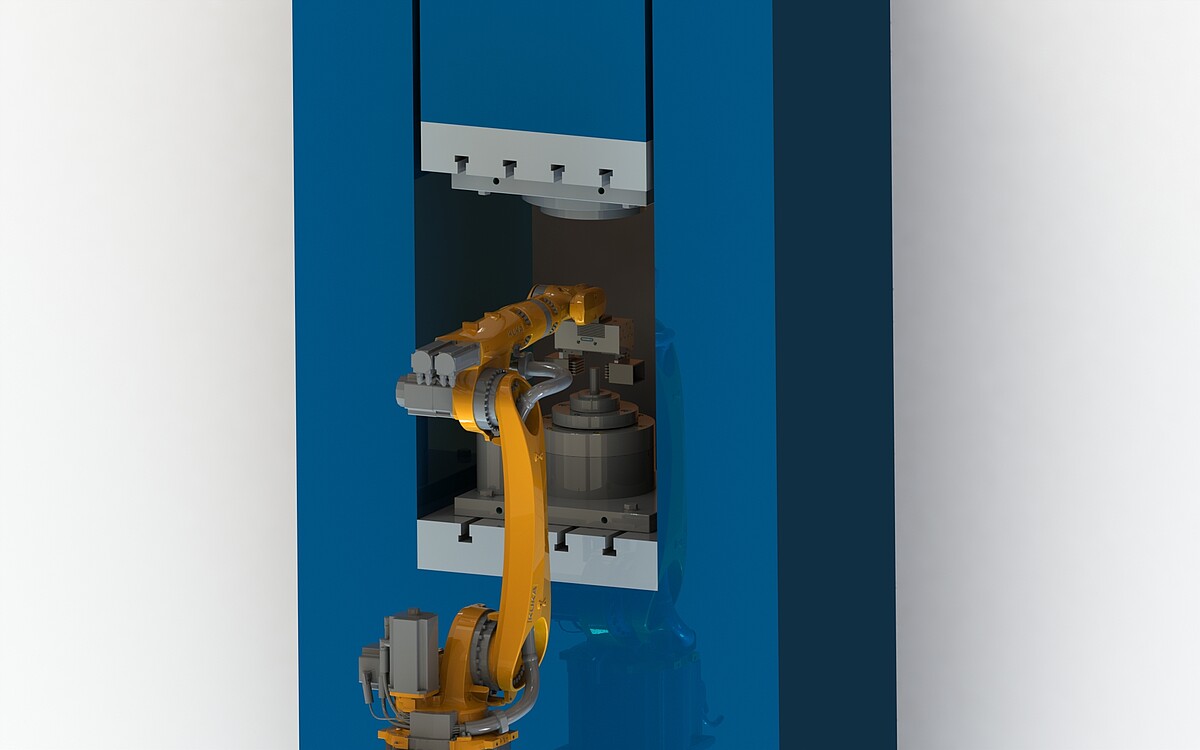
Publications
Subproject leader


30823 Garbsen


30823 Garbsen
Staff
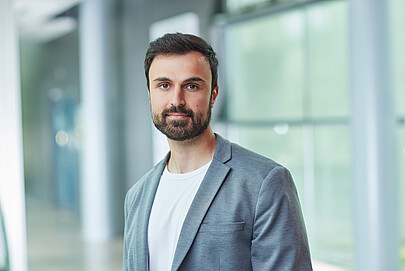
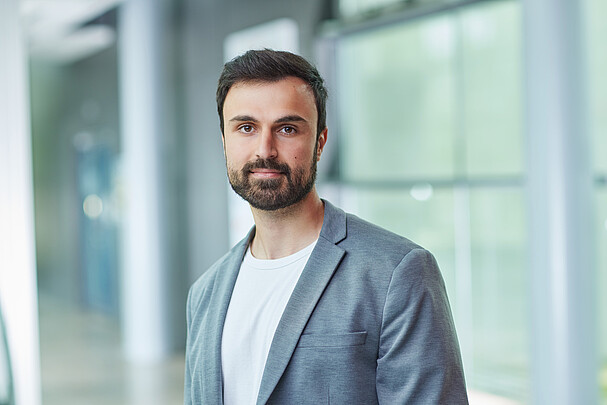
30823 Garbsen
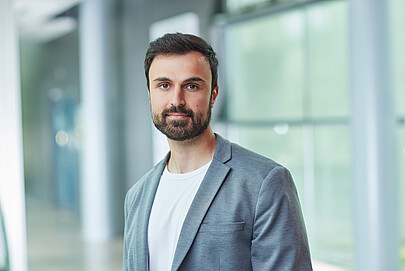
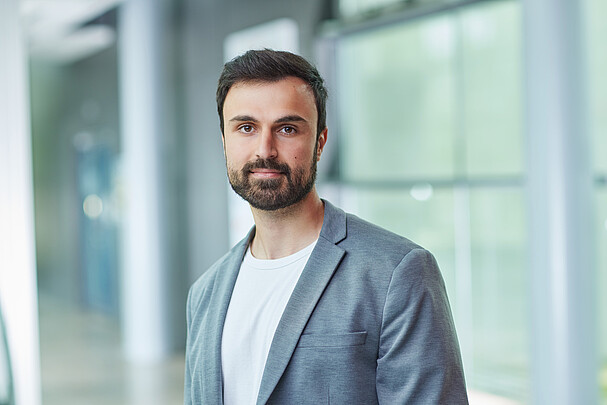
30823 Garbsen