Tailored forming process chain
In contrast to the conventional manufacturing and production processes for hybrid bulk metal components where the joining process only takes place during forming or at the end of the manufacturing chain, the CRC uses semi-finished products that are joined before the forming process. This allows for the production of components that meet the local requirements of different structural and functional areas within themselves much better than mono-material components. By combining different materials within a component, the weight or the costs of the component can be reduced while maintaining or improving performance either by the local use of lightweight materials or by combining it with high-quality alloys. In comparison with the existing manufacturing processes, the simple geometry of the semi-finished products in the tailored forming process chain facilitates handling and a reliable production of a cohesive joining zone. The specifically controlled material flow during the subsequent forming also allows the resulting joining zone geometry to be influenced, which is currently not feasible by the conventional joining processes. The thermomechanical influence during forming also improves the quality of the joining zones.

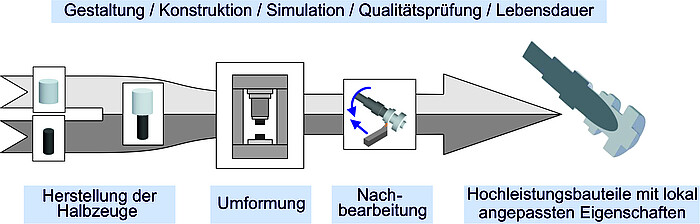
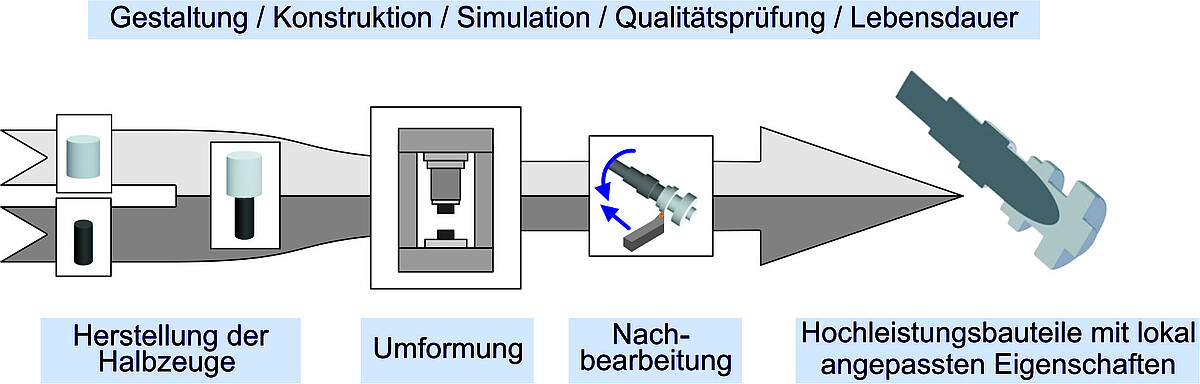
Division in project areas
The innovative approach of the CRC 1153 includes an integral view of the manufacturing and development process from the semi-finished workpiece to the usable component by establishing the necessary process guidelines and deriving specific laws. This includes both fundamental studies on the targeted thermomechanical influencing of material properties during joining and forming, the design and development of novel tool technologies for shaping, and the process-accompanying numerical simulation of manufacturing processes. In addition, questions of post-processing and quality control of the manufactured solid components are dealt with. The subprojects are divided into four project areas