Motivation and objectives
The purpose of subproject C04 is to model the material behavior of the joining zone during tailored forming. On the one hand this incudes the investigation on thermomechanical effects during the tailored forming process. On the other hand subproject C04 investigates the damage and failure mechanics at both, the macroscopic and the microscopic length scale. The results of the microstructural modeling can be used at the macroscopic modeling by doing a homogenization afterwards, compare to figure 1.

Since the development of crystal plasticity and microcracks need information out of the microstructural framework, a multiscale modeling is necessary. Another aim is to investigate the impact of a heat treatment and damage to the forming process. Therefore the focus is set on the coupling effects of the multiphysics within that multiscale framework. The obtained informations about the damage and failure mechanisms at the microstructure are used to model the macroscopic behavior, compare to figure 1. Another aim is to investigate on damage mechanics of a structure made out of the same individual materials (e.g. steel-steel combinations). Therefore a microstructural investigation is not necessary at all. Moreover a modeling of the cooling process during a heating of a hybrid structure, made out of different individual materials (e.g. aluminium-steel combinations), is another key aspect of the second funding period. The overall motivation of this purposes is to give a more precisely prediction of the material response during the forming process and the heat treatment. Additional new computation methods for industrial applications can be provided to ensure a safely use of the hybrid structures.
Results
In the first funding period a model was created to build a computational icrostructure which includes charateristic geometric properties and different phases of the joining zone, refer to figure 2.
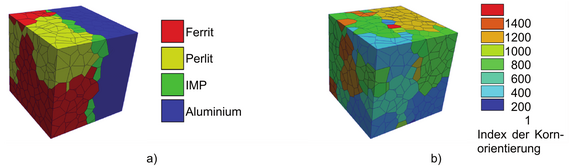
Besides that a new element, based on a cohesive-volume-mixed formulation, was developed during the first funding period, compare to figure 3.
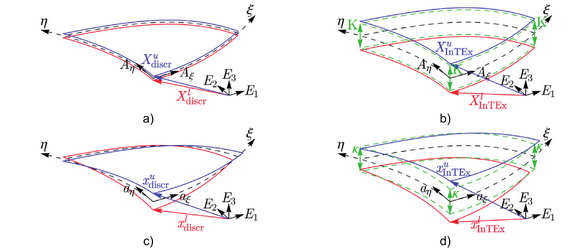
This new element formulation combines the positive aspects of both individual formulations,the cohesive zone element and the volume element. Due to that it was enabled to discretize the intermediate layer at the macroscopic length scale by using flat elements without loosing the ability to compute gradients at that elements. The direction of the extrapolated thickness is given by the normal vector of the cohesive area. Strain measures are computed with respet to the extrapolated geometry, but the connectivity of the element is still given by the non-extrapolated measures. Moreover a phenomenological motivated formulation of damage was developed. Thismodel investigates on the evolution of the areas of the individual bounded parts (e.g. metallic bounded area, intermetallic area and damaged area) during the deformation process, refer to figure 4. The damage is taken into account by a scalar quantity.
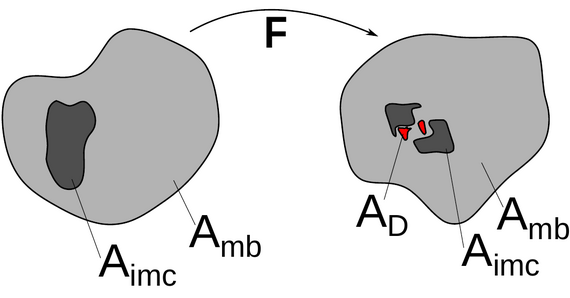
With that it is possible to describe the damage that occurs for instance due to the evolution of the brittle intermetallic part during the forming process. Moreover a micromechanical motivated model for crystal plasticity was developed. This model contains a thermo-elasto-plastic coupled formulation of the material behavior at the crystal lattice scale, based on a dislocation density. This micromechanical investigation leads to a temperature- and strainrate- dependent formulation of the flowstress. Once this quantity is reached, the dislocaions begin to move through the lattice and a plastic deformation of the macroscopic structure occurs.
Current work and outlook
At the beginning of the second funding period the previous discretization of the microstructure is replaced by the new and recently at the IKM developed efficient discretization scheme, called virtual element method (VEM), compare to figure 5.
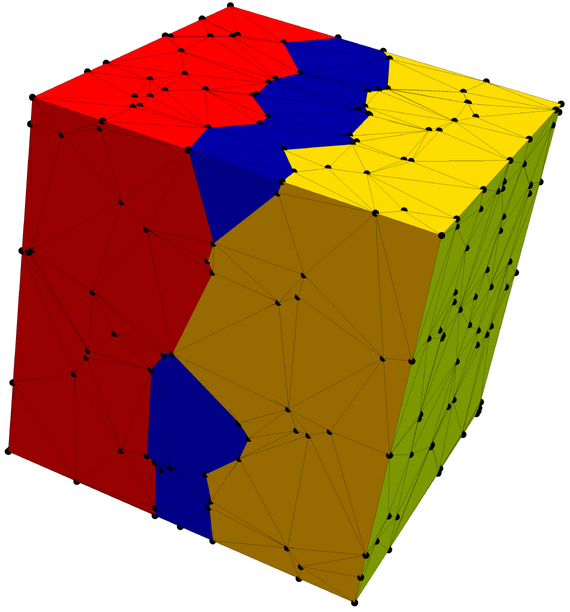
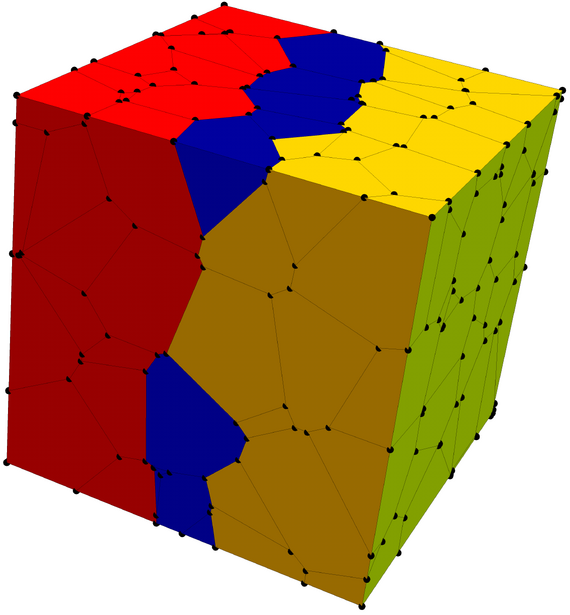
Publications
Subproject leaders

30823 Garbsen

30823 Garbsen
Staff
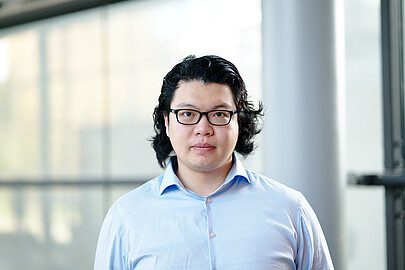
30823 Garbsen
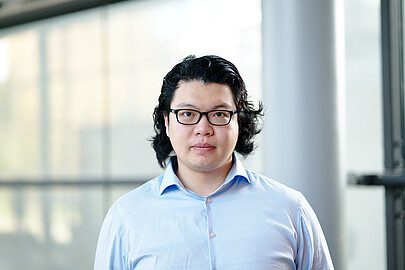
30823 Garbsen